Construction Quality Control Inspections: The Role of Drones
- Geoffrey M Green
- Feb 4
- 6 min read
Updated: Feb 13

In the fast-paced world of construction, ensuring every detail is meticulously checked before final handover is not just a matter of compliance - t's about safeguarding the integrity, safety, and longevity of a building.
Traditionally, this meticulous process has been time-consuming and expensive - often requiring complex setups like scaffolding or cherry pickers. The advent of drone technology is transforming this landscape. Drones are now pivotal in conducting post-construction quality control inspections, offering an unparalleled blend of efficiency, safety, and precision.
Table of Contents
This article delves into how drones streamline and enhance the inspection process of construction projects
1. Aerial Facade Inspections:
Drones can capture high-resolution imagery to spot issues from structural integrity to cosmetic imperfections, ensuring every facet of the facade meets the highest standards before final completion.
Cracked Bricks: Drones equipped with high-resolution cameras can closely inspect facades from various angles, capturing images that can be reviewed to identify areas where caulk or mortar is missing or where brickwork is compromised. This is particularly useful for tall buildings where manual inspection would be both costly and risky.
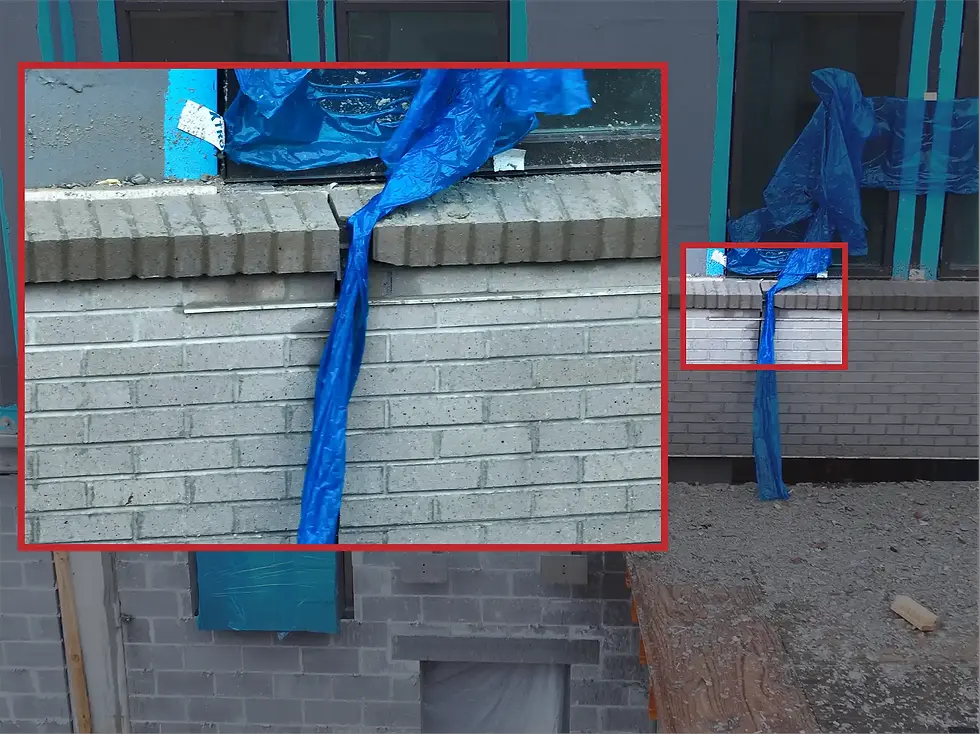
Missing Caulk: Drones can pinpoint where sealant is absent, which is crucial for maintaining the building's waterproofing integrity.
Messy Caulk Work: Drones can document areas where caulk application might be uneven or excessive, which can affect both aesthetics and the building's waterproofing.
Missing Mortar: Similar to missing caulk, this can lead to structural weaknesses and water penetration if not addressed.
Efflorescence: Drones can identify white salt deposits on the masonry surface, which are signs of moisture issues that need correction.
Rust Stains: They can spot rust stains on metal components like window frames or decorative elements, indicating possible corrosion or water leakage.
Surface Irregularities: Drones can detect any bumps, uneven surfaces, or misalignments in cladding or facade panels that might not be visible from the ground.
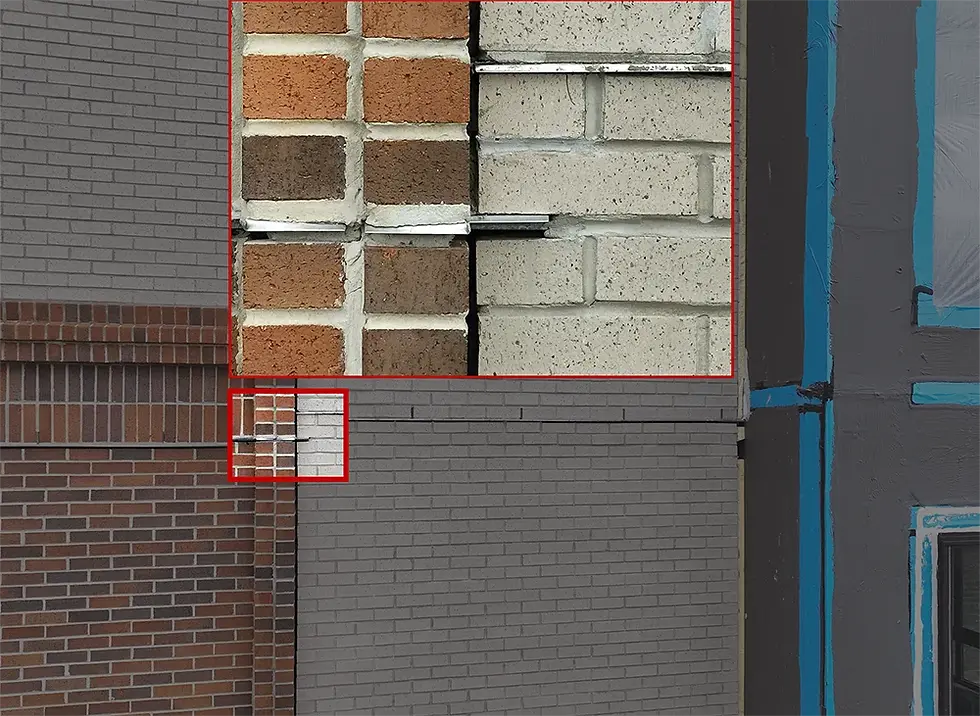
Joint Integrity: Checking the condition of expansion joints for any signs of failure or degradation, which is vital for buildings that expand or contract with temperature changes.
Paint and Coating Defects: Identifying peeling, cracking, or fading of paint or protective coatings, which are essential for both aesthetic and protective purposes.
Facade Panel Attachment: Ensuring that panels or cladding are securely fastened, especially in high-rise constructions where wind forces can be significant.
Graffiti or Damage: Checking for any vandalism or accidental damage that might have occurred during construction, which needs to be addressed before project completion.
Balcony and Parapet Conditions: Inspecting the structural integrity and waterproofing of balconies and parapets, areas often overlooked but critical for safety and aesthetics.
Insulation Cladding: Verifying if the insulation cladding is intact and properly installed, which is crucial for energy efficiency.
Decorative Elements: Examining the condition of architectural details like cornices, moldings, or any decorative facade elements for damage or improper installation.
2. Exterior Window Inspections
Drones can identify a broad spectrum of issues, from compromised seals to installation errors, ensuring that every window enhances rather than detracts from the building's performance and appearance before final sign-off.

Broken Window Seals: Drones can zoom in on windows to check for signs of seal failure, such as condensation between panes or visible cracks. This is crucial for ensuring energy efficiency and preventing water ingress.
Frame Integrity: Drones can inspect for any signs of warping, rust, or damage to window frames, which could compromise the window's functionality or weather resistance.
Glazing Quality: Checking for defects like bubbles, scratches, or distortion in the glass which might affect visibility or safety.
Spacer Bar Condition: For insulated glazing units, drones can examine the condition of spacer bars between glass panes for any signs of deterioration or misalignment.
Weatherstripping: Evaluating the condition of weatherstripping around windows to ensure it's intact and will properly seal against weather elements.
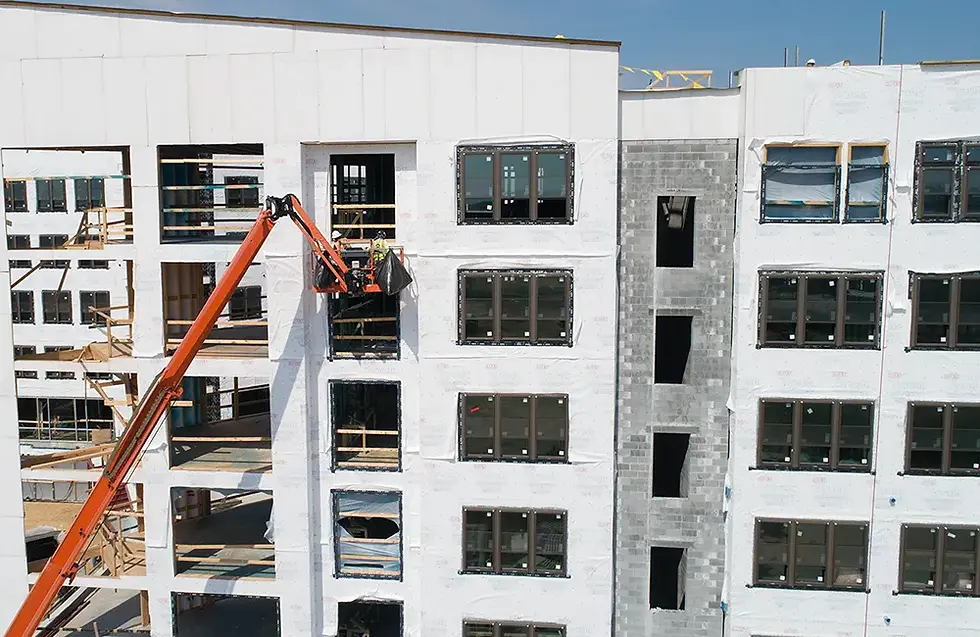
Caulking and Flashing: Checking if caulk around windows is properly applied and if flashing is correctly installed to direct water away from window frames.
Mullion and Transom Inspections: For larger window systems or curtain walls, drones can assess the condition of mullions and transoms for structural integrity and sealant application.
Condensation Issues: Apart from broken seals, drones can look for signs of internal condensation which might indicate poor ventilation or another underlying issue.
External Shading Devices: If windows have external shades, blinds, or sunscreens, drones can verify their proper installation and functionality.
Evidence of Water Damage: Looking for signs like staining or mineral deposits which suggest water leakage or poor drainage.
Insect or Pest Entry Points: Identifying any gaps or cracks around windows that could serve as entry points for insects or pests.
3. Aerial Roof Inspections
From flat to pitched, drones can identify a multitude of issues from membrane integrity to drainage systems, ensuring that the roof is ready to protect the building long after construction is complete.
Tears in the Membrane for Flat Roofs: Drones are ideal for inspecting flat roofs where access might be limited or unsafe. They can document any tears or punctures in the roofing membrane, which could lead to leaks if not addressed.
Brackets Installed Correctly for Roof Membrane: Checking the installation of brackets or supports for membrane systems is vital. Drones can provide a bird's-eye view or close-up angles to verify if brackets are placed correctly and securely.
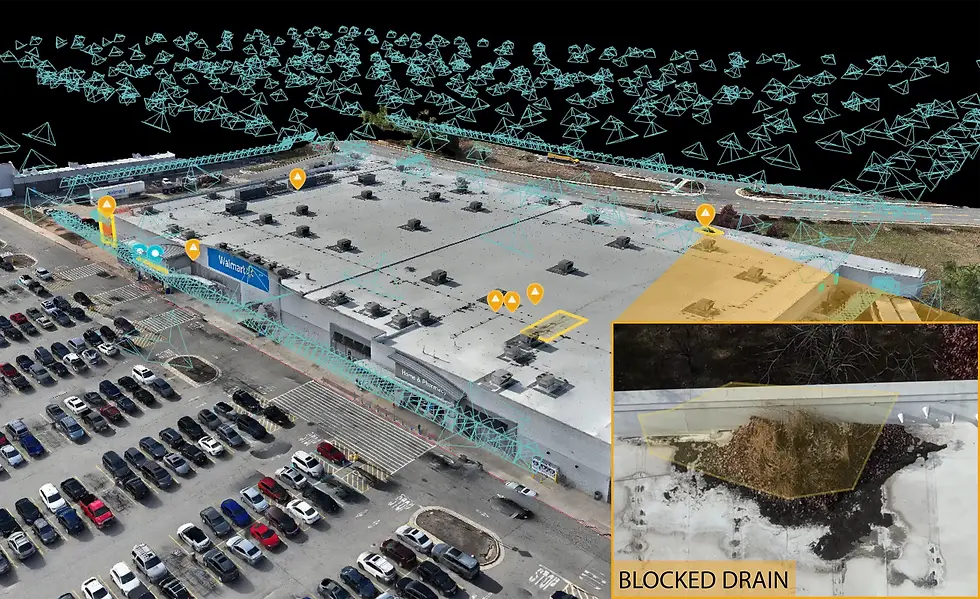
Construction Litter in Drains: After construction, debris can accumulate in drainage systems, especially on roofs with minimal slope. Drones can locate and document this litter, allowing for targeted cleanup before it causes blockages or water accumulation.
Shingle or Tile Condition: For pitched roofs, drones can inspect for missing, cracked, or improperly installed shingles or tiles, which are crucial for waterproofing.
Flashing Integrity: Examining the condition of flashing around chimneys, vents, and skylights for any signs of damage, corrosion, or improper installation.
Sealant Checks: Inspecting sealants around roof penetrations, like vents or HVAC units, for any gaps or degradation that could lead to leaks.
Parapet Wall Condition: Assessing walls around the roof edge for cracks, deterioration, or poor waterproofing which can cause water ingress.
Skylight Installation: Ensuring skylights are installed correctly, with no leaks around their frames or seals.
Vent and Exhaust Systems: Checking if all roof vents, including plumbing and exhaust vents, are in place, sealed, and functioning.
Moss and Algae: Identifying areas where plant growth has accumulated, which can retain moisture and damage roofing materials.
Membrane Ballast: For ballasted roofing systems, drones can check if the ballast (like gravel or pavers) is evenly distributed and not displaced.
Insulation Coverage: On roofs with exposed insulation layers, drones can assess coverage and condition, ensuring there are no gaps or damage.
Signage and Equipment Mounts: Inspecting how signs, satellite dishes, solar panels, or other rooftop equipment are mounted, ensuring they don't compromise the roof's integrity.
4. Customized Reporting
Upon completion of aerial inspections, images and video, captured by the drone, can transform into actionable insights through comprehensive reporting. Here's how this process works:
Data Compilation: All images, videos, and sensor data are collected and sorted. High-resolution imagery is a key component, often paired with thermal or LiDAR data for a more in-depth analysis.
Issue Identification: Each piece of data is meticulously reviewed to spot issues like cracks, missing materials, or misalignments.
Annotation and Documentation: Problems are annotated on images or videos with markers, comments, or overlaid graphics. This includes:
Severity Indicators: Each issue might be categorized by urgency or severity, helping prioritize repairs.
Description: A brief explanation of each issue, possibly including recommended actions for remediation.
Report Generation:
Customized Templates: Reports can be tailored to client specifications, including branding, specific project details, or particular industry standards.
Interactive Elements: Some reports might be interactive, allowing stakeholders to navigate through issues via clickable links or a map interface.
This detailed reporting not only streamlines the process of addressing construction defects but also enhances the relationship between the inspection service provider and the client by providing clear, actionable, and professional documentation. By leveraging technology, such reporting ensures that every minor detail is accounted for, leading to a higher quality end product.
5. Efficiency and Safety
Drone-based inspection services bring a significant transformation to the construction industry, primarily through increased efficiency and enhanced safety. Here's how:
Time Efficiency:
Rapid Inspections: Drones can cover large areas in a fraction of the time it would take for human inspectors, especially for high-rise or sprawling structures. What might take days with traditional methods can often be accomplished in hours.
Reduced Downtime: With less time needed for setup like scaffolding or lifts, construction projects can keep moving forward with fewer interruptions for quality control checks.
Quick Turnaround on Reports: With the data immediately available after flights, reporting can be expedited, allowing for faster decision-making on-site.
Cost Efficiency:
Elimination of Expensive Equipment: Traditional inspections often require significant investment in equipment like cranes, scaffolds, or cherry pickers. Drones bypass these costs.
Labor Costs: Reducing the need for multiple workers to perform high-risk inspections cuts down on labor expenses and potential overtime.
Preventive Maintenance: By catching issues early, drone inspections can prevent costly repairs down the line, contributing to overall project cost management.
Safety Enhancements:
Risk Reduction: The most direct safety benefit is the significant reduction in the need for workers to climb, use ladders, or operate at heights, which are the primary sources of construction accidents.
Consistent Inspections: Drones can be programmed for consistent flight paths, ensuring every inspection is thorough without the variability introduced by human fatigue or oversight.
Conclusion
The integration of drone technology into the construction sector marks a pivotal shift in how quality control inspections are conducted. Not only do drones offer a significant leap in efficiency, allowing for rapid, detailed assessments of building exteriors, facades, windows, and roofs, but they also dramatically enhance safety protocols by minimizing human exposure to hazardous conditions.
This technology transforms time-consuming, costly, and risky manual inspections into a streamlined, cost-effective process that delivers high-quality data and insights. Customized reporting further elevates the value of drone inspections by providing actionable, detailed documentation that directly feeds into the final stages of project completion.
コメント